The market demand for OBCs has increased as the sales of electric vehicles continue to climb. This has prompted manufacturers to make large investments in OBCs, making it the latest product application. This article will explain the development overview of OBCs as well as solutions released by onsemi.
OBCs provide electric cars with long-lasting power
Electric vehicles have become a primary choice when it comes to buying a car, mainly due to the reason that electric vehicles do not emit harmful gases that pollute the environment. With the benefit of obtaining electricity from various primary energy sources including: coal, nuclear energy, and hydropower, etc., people's concerns with respect to a diminishing oil supply can now be put to rest. However, things such as single-trip distance, number of electric vehicle charging stations, and charging speed are still the primary reasons that put people off from buying an electric vehicle. Therefore we need to first improve the charging equipment in order to put the mind of electric car-buyers to ease.
Plug-in hybrid/electric vehicles (xEV) must be externally charged using high-voltage battery subsystems. Some of these are installed inside vehicles (OBC) while others externally, and are allowed to be integrated through wired connected (fixed chargers) or wireless energy transmission (wireless chargers).
Plug-in hybrid electric vehicles (PHEV) are directly equipped with OBCs that are responsible for charging the battery. These chargers are installed within PHEVs, and therefore require high-efficiency and be light-weight, with a range of power levels that correspond directly with battery charging times. The power level of a charger is proportional to the available power of the AC power input (120 VAC, 240 VAC, three-phase, etc.). The most popular power levels for OBCs are 3.3 kW, 6.6 kW, 11 kW, and 22kW, each corresponding with different common AC power levels.
Due to the fact that OBCs are an entirely high-voltage system, the most common semiconductor devices used are IGBTs (Insulated-gate Bipolar Transistors), super junction MOSFETs (Metal–Oxide–Semiconductor Field-effect Transistors) and SiC (Silicon Carbide) in semiconductors. A typical charger consists of many cascaded stages such as: input rectification, power factor correction, DC-DC conversion, isolation, output rectification, and output filtering.
Comprehensive solutions to fulfill the diverse needs of OBCs
Many components are used in the design of OBCs, including SiC MOSFETs, gate drivers, IGBTs, MOSFET modules, IPMs, and controllers. Known for its leading position for power solutions in the industry, onsemi has launched a corresponding product to satisfy OBC application needs.
Here, we recommend 2 suitable SiC MOSFETs for OBCs: NVHL080N120SC1 that supports N-channel design, 1200V, 80 mΩ in TO247-3L packages, and NVBG020N120SC1 that supports N-channel design, 1200V, 20 mΩ in D2PAK-7L package. These 2 SiC MOSFETs both use all new technologies to allow excellent switching performance with a higher reliability than silicon. Furthermore, the low ON resistance and compact chip size ensures low capacitance and gate charge. Hence, the system will benefit from having the highest efficiency, faster operation frequency, increased power density, reduced EMI, and reduced system size.
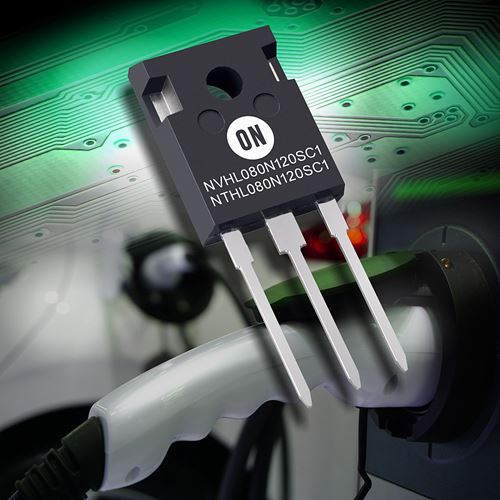
NVHL080N120SC1
NVHL080N120SC1 supports 1200V; when Vgs is 20V, Id is 20A, and the maximum RDS(on) can be 110mΩ while the typical RDS(on) has only 80mΩ. It has high speed switch and low capacitance, passing 100% UIL test, and is in compliance with the AEC-Q101 standard while at the same time Pb-free and a RoHS compliant device. NVHL080N120SC1 can be used in DC/DC converters, vehicle OBCs, and auxiliary motor drives in electric vehicles/plug-in hybrid electric vehicles.
NVHL080N120SC1 supports 1200V; when Vgs is 20V, Id is 60A and the maximum RDS(on) can be 28mΩ. It has high speed switch and low capacitance, passing 100% UIL test, and is a RoHS compliant device in compliance with the AEC-Q101 standard as an automotive-grade device. It can be used in DC/DC converters and automotive inverters in electric vehicles/plug-in hybrid electric vehicles.
Moreover, onsemi has a series of products suitable for OBC application including drivers for SiC MOSFET used in vehicles that support gate drivers - NCV51705 with low-side, single 6A high-speed switching, NCV57001 that has internal galvanic isolation supporting isolated high-current, high-efficiency IGBT gate drivers, and FAN3224TU_F085 with a low-side gate driver that supports dual-channel 4A high-speed switching.
In addition, onsemi also has a series of products for OBC applications, including the NCV51705 gate driver for automotive SiC MOSFETs supporting low-side, single 6A high-speed switching, the NCV57001 gate driver with internal current isolation that supports isolated high-current, high-efficiency IGBT gate drivers, and the FAN3224TU_F085 low-side gate driver that supports dual-channel 4A high-speed switching. The MOSFET module on the other hand has FAM65CR51DZ and is a Power Integrated Module (PIM) with boost converter stage for multi-phase and semi-bridgeless PFCs (power factor correction), and the FAM65HR51DS is a Power Integrated Module (PIM) MOSFET SJ H-Bridge for LLC and Phase-shifted DC-DC Converter.
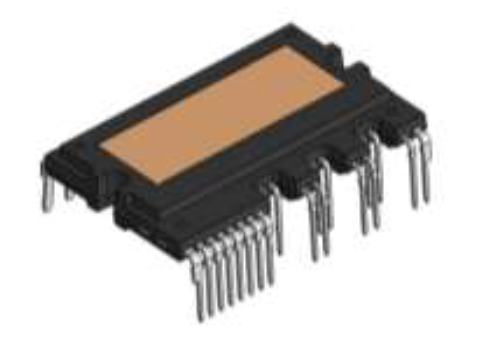
FAM65V05DF1
onsemi has also introduced the FAM65V05DF1, an Intelligent Power Module (IPM) that supports IGBT inverters 650V, 50A. With respect to controllers, there are the NCV3843BV current mode PWM controllers, the NCV1362 Automotive Primary Side PWM Controller for low-power offline SMPS used for low-power SMPS, and the NCV1060/63 used for high-voltage switches for low-power offline SMPS.
Conclusion
onsemi is one of the leaders in terms of power solution and has launched diverse and comprehensive production lines for a variety of OBC specifications and needs, and provides related devices and solutions. As it is the take-off stage for electric vehicles, related application needs are climbing at a fast pace. I trust that you will not want to miss this massive business opportunity.