Ein DC-Motor ist ein elektrisches Gerät, das Gleichstrom in mechanische Bewegung umwandelt. Es existiert eine große Vielfalt von Motoren für die unterschiedlichsten Anwendungen und Leistungsanforderungen, von Kleinstgeräten, die nur wenige Millimeter Durchmesser aufweisen, über medizinische Geräte bis hin zu Sonderanfertigungen, die Tausende PS generieren.
Die am häufigsten eingesetzten DC -Motoren sind bekannt als DC-Bürstenmotoren und DC-Motoren ohne Bürsten (BLDC). Obwohl die zugrunde liegende Physik dieselbe ist, sind ihre Bauweise, ihre Leistungsmerkmale und ihre Steuerungsmethoden sehr unterschiedlich.
Welcher ist der Beste für Ihre Anwendung? Nun, wie so oft im Leben ist die Antwort: „Das kommt ganz drauf an.“ Jeder Motortyp hat seine Vor- und Nachteile. In diesem Abschnitt beschäftigen wir uns mit der Technologie von DC-Motoren und bringen so ein wenig Licht in diese komplexe Thematik.
DC-Motor mit Bürsten Bauweise und Funktionsprinzip
Die im 19. Jahrhundert erfundenen DC-Motoren mit Bürsten sind die einfachste Form von Motoren. Sie waren der erste häufig eingesetzte Motortyp, da sie über die früheren Gleichstromenergieverteilungssysteme für die Beleuchtung betrieben werden konnten.
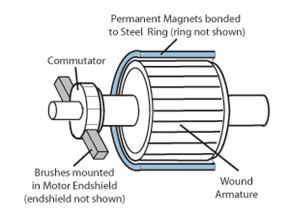
Abbildung 1: DC-Motor mit Bürsten. (Quelle: Oriental Motor)
Wie in Abbildung 1 zu sehen, besteht ein typischer DC-Bürstenmotor aus einem umlaufenden Anker und einer unbeweglichen Spule.
Der Anker (oder Rotor) enthält eine oder mehrere Wicklungen aus isoliertem Draht, der um einen Weicheisenkern gewickelt ist. Die Wicklungen bilden eine oder mehrere Spulen und sind elektrisch mit dem Kommutator verbunden, das ist ein Zylinder aus mehreren metallischen Kontaktsegmenten rund um die Ankerwelle. Der Stator umschließt den Rotor und enthält entweder Permanentmagnete oder Elektromagnete zur Erzeugung eines Magnetfelds. Die Bürsten sind elektrische Kontakte aus einem weichen Material wie zum Beispiel Carbon, sie sind federunterstützt, um mit dem Kommutator Kontakt zu schließen, wenn sich die Welle dreht.
Wenn eine Gleichstromquelle an die Bürsten angeschlossen ist, werden die Ankerspulen erregt, dadurch werden sie zu einem Elektromagneten, sie bewirken die Rotation der Spulen, so dass sich ihre Nord- und Südpole an den jeweiligen Süd- und Nordpol des Stators angleichen. Während der Drehung des Kommutators bewirkt die Bewegung die Umkehrung Polarität des Stroms in der Ankerspule — und der Richtung des Magnetfelds. Der Anker dreht sich zu seiner neuen Ausrichtung, der Strom wird erneut umgekehrt und der Anker dreht sich weiter.
Dieser Vorgang der Stromumkehrung wird als mechanische Kommutierung bezeichnet — die mechanische Rotation der Welle bewirkt das erforderliche Feedback für die Umschaltung der Polarität des Stroms.
Durch Variieren der Anordnung der Wicklungen wurden verschiedene DC-Motortypen entwickelt, die unterschiedliche Leistungsmerkmale aufweisen. Es gibt es fünf verschiedene Grundtypen. Bei den ersten vier Typen befinden sich Spulen sowohl im Stator als auch im Rotor (Anker), es werden also ausschließlich Elektromagneten verwendet.
Bei einem DC-Nebenschlussmotor mit Bürsten sind die Feldspulen von Rotor und Stator parallel angeschlossen; er läuft mit konstanter Drehzahl, unabhängig von der Belastung. Aufgrund dieser selbstregulierenden Funktion wird er häufig für Industrieanwendungen mit konstanter Drehzahl eingesetzt.
Bei einem DC-Reihenschlussmotor mit Bürsten sind die beiden Spulen in Reihen gewickelt; seine Geschwindigkeit variiert je nach der Belastung, nimmt bei zunehmender Belastung ab und bei abnehmender Belastung zu, besitzt jedoch ein sehr hohes Anlaufmoment. daher wird dieser Motortyp häufig für Kurzanwendungen eingesetzt, wie etwa Autoanlasser.
Ein DC-Doppelschlussmotor mit Bürsten ist eine Kombination von Nebenschluss- und Reihenschlussmotor, der Merkmale beider Typen aufweist. Nebenschlussmotoren werden meist eingesetzt, wenn gleichzeitig schwierige Anlaufsituationen bestehen und konstante Drehzahlen erforderlich sind.
Ein separat erregter DC-Bürstenmotor besitzt separate Versorgungen für Rotor und Stator, wodurch sowohl hoher Stator-Feldstrom als auch eine ausreichende Ankerspannung gegeben sind, um den erforderlichen Rotor-Drehmomentstrom zu produzieren. Dieser Motortyp wird verwendet, wenn hohe Drehmomentkapazität und geringe Drehzahlen erforderlich sind.
Ein DC-Permanent-Magnet-Motor mit Bürsten enthält Permanent-Magneten im Stator, wodurch ein externer Feldstrom nicht mehr erforderlich ist. Dieses Design ist kleiner, leichter und energieeffizienter als andere DC-Bürstenmotoren; es wird oft bei Anwendungen mit geringem Stromverbrauch bis zu etwa 2 HP eingesetzt.
Steuerung des DC-Bürstenmotors
Da die Kommutierung mechanisch erfolgt, ist die Steuerung eines DC-Bürstenmotors konzeptionell sehr einfach. Ein Motor mit fester Drehzahl benötigt nur eine DC-Spannung und einen Ein/Aus-Schalter; die Änderung der Spannung bewirkt die Veränderung der Drehzahl über einen weiten Bereich.
Bei Anwendungen, die eine komplexere Steuerung erfordern, kann eine gemeinsame Stromkreistopologie wie die in Abbildung 2 dargestellte H-Brücke verwendet werden. Werden die Transistoren Q1 und Q4 oder Q3 und Q2 simultan eingeschaltet, fließt der Strom des BDC-Motors in die eine oder in die andere Richtung, wodurch eine Bewegung in beide Richtungen möglich ist.
Für die Drehzahlregelung wird ein pulsebreitenmoduliertes (PWM) Signal eingesetzt, um eine Durchschnittsspannung zu erzeugen. Die Motorwicklungen wirken dabei als Tiefpassfilter, so dass eine Hochfrequenz-PWM-Wellenform einen gleichmäßigen Strom in den Motorwicklungen erzeugen kann. Für eine präzisere Drehzahlregelung kann ein Drehzahlgeber wie z.B. ein Hall-Effekt-Geber oder ein optischer Geber verwendet werden, um einen geschlossenen Regelkreis zu bilden.
DC-Bürstenmotoren - Überblick
DC-Bürstenmotoren sind kostengünstig und zuverlässig und haben ein hohes Drehmoment- und Trägheitsverhältnis. Da sie nur wenige oder keine externen Komponenten erfordern, eignen sie sich auch für den Betrieb unter rauen Bedingungen.
Andererseits nutzen sich die Bürsten mit der Zeit ab und verursachen Staub; Motoren mit Bürsten erfordern eine regelmäßige Wartung, bei der die Bürsten gereinigt oder ausgetauscht werden müssen. Andere Nachteile sind eine schlechte Wärmeabführung aufgrund der Einschränkungen des Rotors, eine große Rotorträgheit, geringe maximale Drehzahl und elektromagnetische Störungen (EMI) durch Bürstenfeuer.
Bürstenlose DC-Motor Bauweise und Funktionsprinzip
Das zugrundeliegende Funktionsprinzip eines bürstenlosen DC-Motors (BLDC) entspricht dem eines DC-Bürstenmotors — Kommutierungssteuerung mittels interner Rückmeldung der Wellenposition — aber seine Bauweise unterscheidet sich sehr stark.
Im Gegensatz zum DC-Bürstenmotor wird das Permanent-Magnet am BLDC-Rotor angebracht; der Stator besteht aus genutetem, beschichtetem Stahl und enthält die Spulenwicklungen.
Beim BLDC werden weder Carbonbürsten noch ein mechanischer Kommutator verwendet. Der Rotor wird zur Drehung gezwungen, indem die Spulen um den Stator nacheinander erregt werden. Die Kommutierung erfolgt über einen komplexen elektronischen Controller, der im Zusammenspiel mit einem Rotorlagegeber (z.B. Fototransistor-LED, elektromagnetische oder Hall-Effekt-Geber) verwendet wird.
Die Bauweise des BLDC ermöglicht weniger interne Widerstände und eine deutlich bessere Wärmeableitung als in den Statorspulen. Das führt zu einer verbesserten Betriebseffizienz, da die von den Spulen abgegebenen Wärme über die sehr viel größeren feststehenden Motorgehäuse effizienter abgeleitet werden kann.
Die Statorwicklungen können entweder in Stern- oder Y-Form angelegt werden. Die Stahllaminierung kann genutet oder ungenutet sein. Ein ungenuteter Motor hat eine geringere Induktanz, dadurch kann er mit höheren Drehzahlen laufen und zeigt weniger Restwelligkeit bei niedrigeren Drehzahlen. Der größte Nachteil eines ungenuteten Stators sind seine höheren Kosten, denn er erfordert mehr Wicklungen, um den größeren Luftzwischenraum zu kompensieren.
Die Anzahl der Pole im Rotor kann je nach Anwendung variieren. Durch Erhöhung der Polanzahl wird das Drehmoment erhöht aber die maximale Drehzahl verringert. Auch das für den Bau der Permanent-Magneten verwendete Material hat einen Einfluss auf das maximale Drehmoment, das mit zunehmender Flussdichte ansteigt.
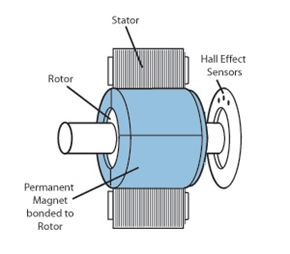
Abbildung 3: Bürstenloser DC-Motor (BLDC). (Quelle: Oriental Motor)
Steuerung des bürstenlosen DC-Motors
Da die Kommutierung elektronisch erfolgen muss, ist die BLDC-Steuerung um einiges komplizierter als die oben beschriebenen einfachen Systeme, und es werden sowohl analoge als auch digitale Steuerungsverfahren eingesetzt. Das Grundmodell eines Steuerblocks ist dem Ansatz eines DC-Bürstenmotors ähnlich, jedoch ist eine Schrittmotorsteuerung unerlässlich.
Ähnliches Produkt:
Es gibt drei Grundtypen für Steuerungsalgorithmen, die für die BLDC-Motorsteuerung eingesetzt werden: Trapez-Kommutierung, Sinus-Kommutierung und Vektor- oder feldorientierte Regelung. Jeder Steueralgorithmus kann auf verschiedene Arten implementiert werden, je nach Codiertechnik und Hardwaredesign, und jede davon bietet bestimmte Vor- und Nachteile.
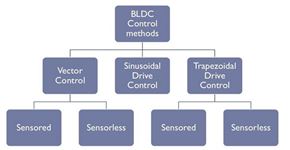
Abbildung 4: Steuerverfahren bei bürstenlosen DC-Motoren.
Für Trapez-Kommutierung sind einfachste Steuerschaltungen und Software erforderlich, daher ist sie ideal für Low-End-Anwendungen. Sie arbeitet in sechs Arbeitsschritten mit Rotorlagerückführung. Trapez-Kommutierung steuert Motordrehzahl und Leistung wirksam, weist jedoch eine Drehmomentwelligkeit auf, besonders bei niedrigen Drehzahlen.
Sensorlose Kommutierung - Bestimmung der Rotorlage durch Messung der Gegen-EMF des Motors - bietet eine dem Hall-Effekt-Verfahren ähnliche Leistung, jedoch auf Kosten einer größeren Komplexität des Algorithmus. Durch Eliminierung der Hall-Effekt-Geber und ihrer Schnittstellenschaltungen verringert die sensorlose Kommutierung die Kosten für Komponenten und Installation und vereinfacht das Systemdesign.
Die Sinus-Kommutierung verwendet die Modulation der Trägerfrequenz, um den Motor anzutreiben, und steuert alle drei Wicklungsströme gleichzeitig, dadurch variieren sie reibungslos und sinusförmig, wenn der Motor läuft. Diese Technik ermöglicht reibungslose und präzise Motoren, da die beim Trapez-Verfahren vorhandene Drehmomentwelligkeit und Kommutierungsspitze eliminiert wurde. Es kann mit offenem oder geschlossenem Regelkreis betrieben werden, mit einem zusätzlichem Drehzahlgeber, und wird häufig für Anwendungen im mittleren Leistungsspektrum eingesetzt, die sowohl eine Drehzahl- als auch eine Drehmomentregelung erfordern. Das komplizierte Schema der Sinus-Kommutierung erfordert für die Implementierung zusätzliche Verarbeitungsleistung und Steuerelektronik.
Die Vektorregelung ist aufgrund ihres komplexen Designs und der hohen Anforderungen, die sie an den Mikrocontroller stellt, dem Bereich High-End-Anwendungen vorbehalten. Der Algorithmus verwendet Phasenstromfeedback zur Berechnung von Spannung und Frequenzvektoren und zur Regelung des Motors. Vektorregelung bietet eine präzise dynamische Regelung von Drehzahl und Drehmoment und ist in vielen Betriebsbereichen effizient.
Auch eine geberlose Technik kann eingesetzt werden. Ein Nebenwiderstand überwacht den Motorstrom und der Algorithmus vergleicht die Ergebnisse mit einem gespeicherten mathematischen Modell der Betriebsparameter des Motors. Dieses Verfahren verringert die Kosten der Messwertgeber, erhöht jedoch deutlich die Anforderungen an den MCU.
BLDC-Steuerungsstrategien im Vergleich
Wie schneiden die verschiedenen Steuerungsstrategien ab? Wie Sie vielleicht erwartet haben. hat der einfache Trapez-Ansatz die schlechteste Drehmomentregelung, verlangt jedoch nicht so viel vom Mikrocontroller oder dem Steuergerät. Am anderen Ende des Spektrums bietet das Vektor-Steuerverfahren (auch feldorientierte Regelung genannt) eine exzellente Regelung von Drehzahl und Drehmoment, aber die Anforderungen an den Mikrocontroller sind hoch.
BLDC Zusammenfassung
Ohne einen mechanischen Kommutator oder Bürsten, die sich abnutzen, erfordern bürstenlose DC-Motoren nur geringen Wartungsaufwand und sind nicht funkend. Zudem haben sie eine geringere Wellenreibung und Trägheit, machen ein weniger hörbares Geräusch, weisen ein deutlich besseres Drehmoment-Gewichtsverhältnis (Leistungsdichte) auf, dadurch sind sie sehr viel kleiner als ein vergleichbarer DC-Bürstenmotor.
Verglichen mit DC-Bürstenmotoren bieten BLDC-Motoren etliche Leistungsvorteile. Sie haben einen hohen Anlaufmoment, das Drehmoment ist flach bis zur Nenndrehzahl. Aufgrund der verzugslosen elektronischen Steuerung ist ihre Drehzahlregelung präzise und unempfindlich gegen Lastschwankungen. Da die Wärme im externen Stator erzeugt wird und nicht im internen Rotor, sind sie einfacher kühl zu halten. Das Fehlen von Bürsten bedeutet, dass sie weniger elektrisches Rauschen produzieren und mit höheren Drehzahlen laufen können — in einigen Fällen mit bis zu 100 000 U/Min.
Verfügbare DC-Motorsteuerungslösungen
Wie gezeigt wurde, ist eine einfache DC-Bürstenmotorsteuerung einfach zu haben, präzisere BDC-Steuerung und BLDC-Steuerung sind beide alles andere als unkompliziert.
Die gute Nachricht ist, dass viele Standardlösungen angeboten werden, die zu Motoren mit geeigneten Reglern passen. Auf Geräteebene bietet Arrow Electronics zahlreiche Motorregler führender Hersteller sowohl für DC-Motoren mit als auch ohne Bürsten. Da es sich bei der Motorsteuerung um einen riesigen Markt handelt, bieten viele Hersteller Entwicklungskits, Referenzdesigns und Softwarebibliotheken an, die auf die DC-Motorsteuerung ausgerichtet sind.
Fazit: Welcher ist der Beste für Sie?
Ihnen steht eine große Auswahl zur Verfügung, aus der Sie je nach Anwendung die passende Technologie Ihres DC-Motors wählen können.
Wie wäre es mit einem platzbeschränkten medizinischen Gerät, bei dem Wartung keine Option ist? Suchen Sie zunächst bei bürstenlosen Anwendungen. Ist Ihr Hauptanliegen eine kostengünstige Lösung? Dann ist ein DC-Permanent-Magnet-Motor das Richtige für Sie.
Sie benötigen eine sehr präzise Steuerung? Wählen Sie einen BLDC, vielleicht mit einer digitalen Steuerungsstrategie. Ein einfaches Regelungsschema? Suchen Sie nach einem DC-Bürstenmotor.
So oder so, da Sie jetzt die jeweiligen Vorzüge der verschiedenen Technologien verstehen, dürften Sie in einer besseren Position sein, um die richtige Wahl zu treffen.